In this article, we will discuss harmonic vibrations in automotive drivetrains. While they are inherent in drivetrain operation, uncontrolled vibrations can lead to increased wear, drivability issues, disruptions to electrical sensors such as accelerometers, and severe transmission case damage.
Harmonic vibrations occur when the components resonate at their natural frequencies, resulting in oscillations. These vibrations come from various sources, including the engine, transmission, driveshaft, differential, tires, and wheels. Each rotational component has its own set of natural frequencies, and when frequencies of multiple components align, vibration is amplified. Just the same if the frequency is offset, then vibration is reduced. Frequencies can be measured in HZ and amplitude, so you can measure the amount of vibration being produced. This can be useful in identifying the culprit of an unwanted harmonic vibration.
Torsional is one common type of harmonic vibration in the drivetrain. Torsional vibrations involve the twisting motion of the drivetrain components, such as the crankshaft and driveshaft. The repeated oscillations place stress on these parts, leading to material fatigue and potential failure over time.
These vibrations may be due to the firing pulses in the engine cylinders or sudden changes in torque demand. If not addressed, torsional vibrations can lead to several detrimental effects.
To address the damage potential caused by harmonic vibrations, automotive engineers use dampers or vibration absorbers. These are designed to absorb and dissipate the energy of the vibrations, reducing their impact on the drivetrain components. Dampers can be in the form of rubber mounts, harmonic balancers, or tuned mass density weights, depending on the specific application.
For example, an internal combustion engine uses a harmonic balancer bolted to the end of the crankshaft to smooth the firing pulses. If the dampener was missing the engine would self-destruct due to the vibration. Some drive shafts have a similar external style balancer for the same reason.
Harmonic vibrations can also affect the overall drivability and performance of the vehicle. The vibrations can create an uncomfortable driving experience, causing excessive noise, vibration, and harshness (NVH) levels in the cabin. This not only reduces comfort for the occupants but can also negatively impact the vehicle's handling and stability.
Let's look at contributors of bad vibrations that are out of factory specification starting with driveline angles. The universal joints(u-joint) allow the transfer of torque through a shaft that is not in line with the component it is transferring the torque into. However, the two components being connected need to be on the same axis for the u-joint working angles to cancel each other out. The angles need to cancel each other out or you will feel the u joint speed up and slow down continuously through its rotation. This oscillation in speed will cause an unwelcome harmonic vibration.
Spicer garage video showcasing u-joint speed variance in relation to the working angle:
This is an ideal driveline angle. In this representation of drive line angles, you will see the axis plane of the transmission output shaft and the pinion gear input shaft are equal and the driveshaft/u-joints offset each other. Parallel.
In this representation, you see an exaggeration of what happens when torque is applied to the driveline. In this situation, the angles don't offset each other while accelerating from a stop, which will result in a vibration in the driveline.
To compensate for the expected rotation when torque is applied, our pinion angle from the factory may be set slightly down (about 1/2* - 1) while static, and the suspension is loaded with the full vehicle weight. This is common in leaf-sprung suspensions because they are more susceptible to axle rotation.
Due to variances in suspension design and other factors, this is only a general representation. For vehicle-specific specifications and adjustment points, refer to the factory manual. A lot of factory suspensions do not have an adjustment for this. If the measurement is out of specification look for worn or damaged components such as:
- Mounts for the engine or the transmission
- Cross members
- Frame
- Control/Trailing arms
- Leaf springs or leaf spring hangers
- Carrier bearing
Just as misalignment can cause a vibration, a failed u-joint may do the same. U-joints can fail in several ways. When checking for a bad U-joint I commonly see technicians grab the driveshaft while it is installed in the vehicle and push up and down on it. If there is no play they deem the U-joint good. This is a horrible way to determine the state of the U-joints. The only way to properly check this is to remove the drive shaft, or axle and move the joint through its entire range of motion without a torsional load on it. For reference here is a photo courtesy of Spicer showing the construction of a simple U-joint.
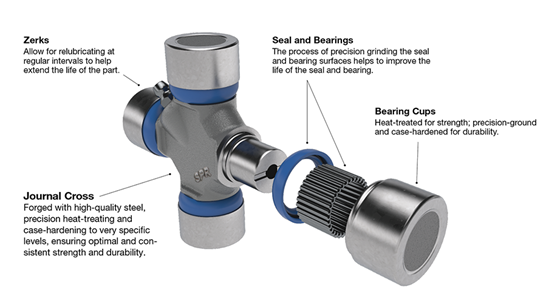
The most common and obvious failure is when the needle bearings are falling out of the caps and there is a lot of play. This is because there is nothing between the cap and the journal cross. There are other failures that are less obvious and cause just as much driveline vibration. If there is binding due to abnormal wear on the journal or a seized cap you will also have a serious vibration. To check for this, you must rotate the u-joint through its entire range of motion and ensure the bearing is smooth. If it feels "notchy" or it sticks at any time, you may need to replace the joint. If this is a greaseable style joint (look for a Zerk) try adding grease. After adding grease work the joint and see if the action is smooth. If you cannot add grease or the grease didn't improve it, you will need to replace the joint.
Another commonly overlooked item is the splines of the drive shaft. For the suspension to work properly the drive shaft is required to extend and retract continuously while driving down the road. See the photos below.
With the suspension in this position, the drive shaft must extend to its maximum length due to the arch that the differential travels. In this illustration, the length of the trailing arms and the fixed points that they are attached to determine the shape of the arch. This will vary in different suspension designs.
When the suspension travels in its range of motion, the arch it travels in forces the drive shaft to retract.
It is very important that the splines aren't seized because the aluminum transmission case since it is the weakest when compared to a cast iron differential, steal trailing arms, and cast-iron engine block, and it will break from the force of the suspension traveling in its designed path.
Balance can also be the cause of harmonic vibration. Tires and wheels should be considered as a source of vibration, the bigger the tire and wheel combo the higher the amplitude of the vibration. If you have ever tried to balance a set of big mud tires you know exactly what I'm saying, most of the time it is impossible to balance them without adding all the weights you have in the shop. The same can be said for unwanted weight such as ice, or mud buildup in the wheels.
It is important to point out that the drive shaft spins much faster than these components, due to gear ratio it spins 3 to 4 times faster than the Tires, Wheels, and Axles. This is why it is important to visually inspect these items. Look for signs of impact and/or anything that is not there by design. It may be helpful to measure runout with a dial indicator as well.
It is common to have the drive shaft balanced if you suspect it is the source of a vibration. Any drive shaft shop should be able to check and fix this, a lot of the time they find new OE shafts out of balance, so it is a good idea to have it checked.
In summary, these often-overlooked items can wreck your day if left unchecked. Hopefully, this basic understanding of how these items work together and what to look for will help deliver a better product to your customer and keep your bays turning new work.